Â
Customer Profile
- Customer: RAMCAR Technology Inc.
- Industry: Automotive
- Solution: Moldex3D Advanced
- Country: Philippines
The company started in 1988 as the machine shop department of the RAMCAR Inc. battery plant in Meycauayan, Bulacan. It was originally set up to do the repair and maintenance work for the production department’s equipment. The group was later spun off into a separate company, Ramcar Technology, Inc. and became the provider of quality molds, tooling, and equipment for the automotive, motorcycle, and industrial battery industry. (Source: www.ramcartechnology.com)
Executive Summary
RAMCAR Technology is the provider of quality molds, tooling and equipment for manufacturers of automotive, motorcycle, and industrial battery products. Over the years, RAMCAR Technology has strived to become the leader in the industry by continuous upgrading its capability through investments in industrial equipment and the development of world-class products. One of the most important investments is to deploy Moldex3D injection molding simulation software. The implementation of Moldex3D has made a significant impact on RAMCAR Technology’s capability to produce the best quality products at minimum cost and time.
Challenges
- Unbalanced flow in two-cavity and multi-gate System
- Non-uniform part thickness
- Unacceptable warpage
- Flash caused by overpacking
Solutions
The implementation of Moldex3D CAE simulation software has allowed RAMCAR Technology to identify the real design problem in software without actual tooling. With that, RAMCAR Technology is able to reduce costly design changes and increase productivity.
Results
- Improved cycle time by 16%
- Raised productivity by 40%
Case Study
The pinhole on the partition caused the battery container to fail the electrolysis test
This case has demonstrated how RAMCAR Technology leveraged Moldex3D simulation software to successfully validate the real design problem of the battery container and determine the best approach to produce the part.
The battery container part was facing a very high rejection rates and failed the die electrolysis test. Moldex3D simulation helped the RAMCAR Technology team better understand the reasons behind the product defects by visualizing the flow behavior through the part. Through the filling analysis, the pinhole issue was found on the upper part of the partition wall.
Using Moldex3D’s filling simulation helped identify the pinhole in the upper part of the partition wall.
After identifying the challenges the pinhole posed for product quality, the team needed to find the best solution to eliminate the pinhole in the shortest time possible. Since it’s an existing product, the less revision needed to be made the better; otherwise, the mold, the tooling, the process and other components might also be affected.
RAMCAR Technology team came up with four different solutions to this problem:
   1. Parameter/Process Condition Adjustment
   2. Mold design revision
   3. Product design alteration
   4. Mold design revision and product design alteration
If RAMCAR Technology had to construct physical prototypes to test each solution, they would have to spend a great deal of time and money. Moldex3D enabled RAMCAR Technology to test and scrutinize each solution thoroughly in software without actual tooling. With the help of Moldex3D, RAMCAR team could simulate proposed design changes with optimized parameters and compare analysis results to determine the best approach to adopt. After comparing multiple runs, Moldex3D showed and validated that increasing gate size is the simplest and best solution to achieve and satisfy customer requirement in flow balancing and address problem of short shot, weld line, flashing at skirt portion and minimizing sink mark.
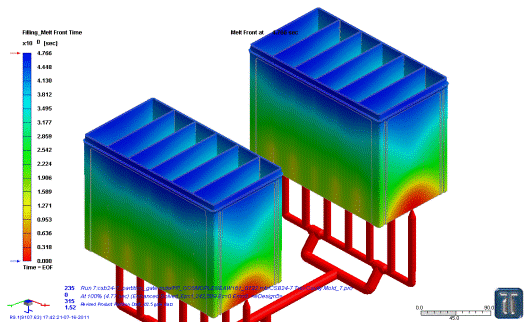
Using Moldex3D to try different design changes and compare and visualize simulation results without building real parts. The simulation results showed filling delay problem (left) and a more balanced flow pattern (right).
 |
Filling |
Packing |
Cooling |
Mold Open |
Total Cycle Time |
Cycle Time Improvement |
Existing Cycle Time |
5 sec |
6 sec |
26 sec |
5 sec |
42 sec |
Decreased by 16% |
Adjusted Cycle Time |
5 sec |
3 sec |
22 sec |
5 sec |
35 sec |
The cycle time comparison between the existing mold and the optimized design
Cycle Time |
Production/hr |
Productivity Improvement |
Existing Cycle Time:
42 sec (2 cavities) |
145Â pieces |
Improved by 41.3% |
Adjusted Cycle Time:
35 sec (2 cavities) |
205Â pieces |
The production rate comparison between the existing mold and the optimized design
Saving money and time while achieving higher quality
Using Moldex3D simulation, Ramcar Technology eliminated the multiple design issues of the battery container, such as the flow imbalance, pinhole and flash. Moldex3D also helped RAMCAR Technology optimize the whole process and improve the productivity. Through simulation the following results have been achieved:
- Improvement of the X-displacement by 30% – the warpage is within tolerance
- Reduction of the packing time by 50% – achieving balanced flow
- Elimination of the pin hole and the visible weld line
- Elimination of the post molding process – no more flash occurrence
- Productivity increased by 41.3% due to reducing cycle time by 16%
- No more rejection of the parts at the electrolysis die test
Today, RAMCAR Technology uses Moldex3D to reduce product development cost and time while improving the quality of the products. The predictive capability of Moldex3D has progressed to the point where much of the design verification is now done using simulations rather than physical prototype testing. RAMCAR Technology is planning to expand current Moldex3D simulation applications to large plastic parts such as industrial battery components.
Oil Press 120 Model
almond oil press machine
Oil Press Machine,Peanut Oil Machine,Oil Making Machine,Almond Oil Press Machine
Mianyang Xinyu Agricultural Machinery Manufacturing Co. , https://www.xyoilpress.com