Sea Mi ladder magnetic pump is from Dalian Sea Mi Le sealed Pump Co., Ltd. production. The pump design advanced, no shaft seal, as a leak-free, maintenance-free, reliable and reliable centrifugal pump, with safety, efficiency, energy saving features. For transporting corrosive, toxic, flammable, explosive, expensive or easy to vaporize liquids. In addition, the sea-Mile ladder magnetic pump is also suitable for transporting high-temperature, low-temperature fluids and liquids under vacuum. Due to its completely leak-free advantages, it has successfully solved the problems of running, running, dripping and leaking in fluid transportation. It has become an irreplaceable product in environmental engineering and is widely used in petroleum, chemical, refrigeration, air-conditioning, aerospace, etc. In the field.
Compared with the traditional seal pump, sea Mirage gram magnetic pump with a maintenance workload is small, without external lubrication, no leakage, vibration, noise and other advantages. However, due to its own characteristics in many ways it is different from the traditional centrifugal pump, so in the process, installation, operation and so take some measures and ways to ensure its reliable and smooth operation.
Sea Mi ladder magnetic pump features
1. Structure: Sea-Mile ladder magnetic pump is axial suction, radial discharge of horizontal completely leak-free centrifugal pump, the shaft through the magnetic coupling drive, no rotary shaft seal device, sea Mirage gram magnetic pump to achieve "zero leakage ".
2. Bearings: Sea-Mile ladder magnetic drive shaft through the rolling bearing bearings, rolling bearings lubricated by its own grease; pump shaft through the hydraulic sliding bearings.
3. Magnetic coupling: Sea Mirage Keke magnetic pump magnetic block is a high-quality rare earth permanent magnet materials, the maximum irreversible temperature up to 350-400 ℃, fully guaranteed the magnetic coupling with reliable performance. Normal work, the magnetic coupling and three-phase asynchronous motor synchronous operation, stable performance. And permanent magnets are highly stable and prevent the adverse effects of assembling and disassembling the rotor or operating the pump at maximum torque.
4. Lubrication of sliding bearings and cooling of magnetic couplings: The medium delivered by the pump is lubricated and cooled without the need for external lubrication and cooling water systems.
5. Axial force balance: At work, the axial force of the magnetic MiTAC magnetic pump is automatically balanced by the hydraulic force to drive the disk to withstand instantaneous axial thrust when starting and stopping.
Analysis of Common Malfunction of Sealed Ladle Magnetic Pump
1. Pump operating conditions caused by fluctuations in a large problem: Sea Mirage magnetic pump axial force is automatically balanced by hydraulic equilibrium. In the actual operation, if the operating parameters (inlet pressure, outlet pressure) fluctuations, it is easy to damage the magnetic Mihai Gravity magnetic pump balance, so that the bearing to bear the large radial and axial load bearing damage caused.
2. Pump cavitation caused by the problem: Pump cavitation causes mainly pump inlet tube resistance, medium more gas, filling pump is not sufficient, the pump inlet can not enough and other reasons. Cavitation is the most damaging to the pump. In case of cavitation, the pump vibrates violently and the hydraulic balance will be severely damaged, which will damage the pump bearing, rotor or impeller. This is a common cause of Malcolm magnetic pump failure.
3. No medium or medium flow rate is small: dry friction bearings, burning bearings. Sea-Mile ladder magnetic pump is provided by the transmission medium to the lubrication and cooling of the sliding bearing, without opening the valve or the outlet valve in the case of sliding bearings due to non-transmission medium lubrication and cooling damage.
4. Isolation sleeve damage: Sea-Mile ladder magnetic pump magnetic coupling is transported by the pump medium cooling, if the medium with hard particles, it is easy to cause the isolation sleeve scratched or scratched, and sometimes improper maintenance methods may also be Caused by the isolation sleeve damage.
Ways and Means to Improve Operation Reliability of Magnetic Seal Pump
1. Equipment and piping installation requirements:
(1) The pump inlet and outlet piping shall be supported so as to prevent the transfer of extra loads to the pump. The pump shall not be used as a point of force in the piping and the piping system shall be compensated for thermal expansion.
(2) When the suction head is low, the inlet piping should be as short as possible to prevent cavitation. The inlet pipe should be of suitable size to ensure that the fluid flow rate does not exceed 3m / s; when conveying easily vaporized fluid or liquefied gas, the flow rate shall not exceed 3m / s; when conveying easily vaporized fluid or liquefied gas, the flow velocity shall be ensured Not more than 1m / s.
(3) The outlet pipe should be installed with a control valve to adjust the pump flow and lift. When using longer outlet lines or when using two pumps in parallel, it is advisable to install an additional one-way check valve.
(4) The entire piping system and auxiliary piping should be carefully cleaned to prevent iron filings, welding slag or other foreign matter from entering the sea-gravel magnetic pump. For new piping systems, the inlet piping should be equipped with filters.
(5) The piping design should take into account the pump exhaust.
(6) In order to realize the continuous operation of the pump, it is suggested to install a return pipe and install the minimum flow orifice to ensure sufficient lubrication and cooling of the plain bearing during continuous operation.
As shown in Figure 1, the return line should be drawn from the outlet valve or one-way check valve and returned to the reservoir through the minimum flow orifice. This installation allows automatic pump exhaust.
(7) Sea-Mile ladder magnetic pump must work within the specified range. To control the maximum flow rate, it is advisable to install a suitable maximum flow orifice in the outlet line.
2. Process monitoring:
Due to the design characteristics of magnetic seal ladder magnetic pump, generally do not need maintenance, but in order to ensure its normal operation and safety, should use the process monitoring device, strict management.
(1) Entry tank level protection control is necessary, the inlet tank should be equipped with a level transmitter or level switch, the inlet tank level is reduced to a certain extent, the pump will automatically stop the operation to protect the pump.
(2) The pump body shall be equipped with a temperature sensor to monitor the temperature of the magnetic stator and pump bearing to protect the bearings and the magnetic stator.
(3) Pump outlet should be equipped with level control valve, according to the level of the inlet tank to regulate the delivery of media displacement.
(4) Differential pressure sensors and switches should be installed to measure the pressure difference between the outlet of the pump and the inlet. When the differential pressure is lower than the set value, the pump will stop automatically and play the role of protecting the pump.
(5) The vibration of the pump is extremely small, and the large vibration and noise explain the malfunction.
(6) In order to ensure normal work, should ensure that the pump in the flow and lift shown in Figure 2 within the scope of work, the minimum and maximum working flow, head in the performance curve are described.
(7) In order to avoid cavitation, the Hamiltonian magnetic pump requires a minimum suction pressure (emin) for delivery of easily vaporized fluids and is calculated as: (emin) (m) = NPSH pump (m) Friction loss (m) + safety margin (m), safety margin is usually 0.5m.
3. Operation points:
(1) perfusion and exhaust:
In order for the sea-Mile ladder magnetic pump can be normal operation, you must fully perfusion and exhaust. The pump inlet pipe and return pipe, the outlet pipe valve fully open, you can achieve dense ladder gram magnetic pump automatic exhaust.
When transporting liquefied gas or easily vaporized liquid, evacuate several times until the pump is full of liquid. If cryogenic liquid is to be delivered, wait until the overcurrent component of the pump cools to the temperature of the liquid before starting, which ensures that the fluid has reached the pump sections.
(2) start the program
Magnetic coupling model is based on the choice of the drive motor to achieve normal operation, but start in case of discomfort (such as motor power is too large, the outlet valve is open too much or a higher voltage, etc.), will exceed the magnetic linkage The maximum torque of the shaft, so that the pump can not be normal operation, so be careful to start correctly.
a. Fully open the inlet line valve;
b. close the outlet pipe valve;
c. Start the motor;
d. Slowly open the valve in the outlet line;
e. Adjust the outlet valve until it reaches normal operating pressure;
f. For proper pump operation, allow the pump to work within its allowable range.
Operation and maintenance precautions:
1. Sea-Mile ladder magnetic pump absolutely not allowed in the dry friction state and the export pipeline valve closed work, otherwise it will lead to sliding bearing damage!
2. Must work in synchronization with the motor, if the pump failure (head is small), it indicates that the magnetic coupling has exceeded the maximum torque, should avoid prolonged work in the unpleasant conditions.
3. Under normal working conditions, vibration, greater noise and power increase, indicating bearing wear (lack of lubrication) should be checked immediately.
4. Sea Mirage gram magnetic pump rolling power bearings for deep groove ball bearings, by its own grease for permanent lubrication, but also regular inspections, regular replacement.
5. Magnetic coupling failure does not mean that the permanent magnet damage. However, in the failure of a long time to work because of its low speed, poor lubrication of plain bearings, will lead to the sliding bearing damage.
6. The rotor assembly and the drive assembly have high magnetic properties. When assembling and disassembling the viscous magnetic pump, the magnetic force range should be taken into consideration. It may have some impact on the power and electronic devices, and should be kept at a certain distance
7. When placed for extended periods of time, if the liquid being delivered will crystallize or solidify, flush the pump with the appropriate fluid.
CNC Milling
In general, computer numerical control milling machine (CNC) machining is a deductive manufacturing technique that programs 3-axis linkage, complex to 5-axis linkage, drives milling cutters to remove layers from solid blocks called blanks to produce finished parts. CNC milling is one of the main types of CNC Machining, which uses cutting tools that rotate at a speed of several thousand to tens of thousands of revolutions per minute (RPM) to precisely remove materials to obtain parts with complex surfaces. In addition to milling, CNC machining is also equipped with drills, boring tools, thread cutters and other tools to complete different part features at once. CNC machining produces parts based on a computer-aided design (CAD) model that is sent to a CNC machine through computer-aided manufacturing (CAM) software.
CNC Machining centers developed from CNC milling machines. The biggest difference compare to CNC milling machines is that the machining center has the ability to automatically exchange machining tools, by installing tools for different purposes on the tool magazine, the machining tools on the spindle can be changed through the automatic tool changing device in a single clamping device to achieve a variety of machining functions.
CNC Milling Finish
|
|
Process
|
Roughness Ra(um)
|
Cylindrical milling cutter milling (rough)
|
12.5~3.2
|
Cylindrical milling cutter (fine)
|
3.2~0.8
|
Cylindrical milling cutter (precision)
|
0.8~0.4
|
Cylindrical milling cutter (rough)
|
12.5~3.2
|
Cylindrical milling cutter milling (fine)
|
3.2~0.8
|
Cylindrical milling cutter milling (precision)
|
0.8~0.4
|
Cutter milling (fine)
|
12.5~3.2
|
End milling cutter (rough)
|
3.2~0.4
|
End milling cutter (precision)
|
0.8~0.2
|
High speed milling (rough)
|
1.6~0.8
|
High speed milling (fine)
|
0.4~0.2
|
CNC milling accuracy
CNC milling centers and high-Precision Machining centers. Ordinary machining center, resolution of 1μm, maximum feed speed of 15 ~ 25m / min, positioning accuracy of about 0μm. High-precision machining center, resolution of 0.1μm, maximum feed speed of 15 ~ 100m / min, positioning accuracy of about 2μm. Between 2 and 10 μm, with a ± 5 μm more, can be called precision grade. FCE equipped with different grade and different size CNC milling center. Take in to account into both economic and quality in parallel.
CNC Finishing surface treatment
Post-processing is the final step in the CNC machining process. In a quick guide, we offer a lot of surface treatments to complete your final parts and get them to meet strict specific requirements. It should be noted that in CNC machining, post-processing is in optional, as the quality of the machined parts is already very high.
Anodized
The anodizing process allows the part to obtain excellent corrosion resistance, increasing the hardness and wear resistance of the surface. Anodizing is also the most common pre-painting treatment, which can help the painted surface to obtain good adhesion. We typically apply two types of anodizing in our production: Type II, corrosion resistant; Type III is thicker, adding a layer of wear resistance. Both anodizing processes can achieve a variety of color effects.
Polishing
Grinding polish, it offers the fastest turnaround parts and does not require post-processing. The surface finish of the grinding part is equivalent to 125 um in Ra, and the requirements can be increased to 63, 32 or 16 um Ra. Minor tool marks may still be visible on the last part.
Powder coatings
Powder Coating is thermoplastic powder spraying directly on the processed part. The sprayed parts are then baked in an oven to form a durable, abrasion- and corrosion-resistant plastic coating. In the powder coating process, its color, brightness, surface roughness can be customized.
Shot blasting
Shot peening is the high-speed spraying of beads of different hardnesses and sizes onto the surface of the part. To get different textures and brightness of the surface. Since the surface has been hit by similar forging beads, the hardness and wear resistance of the surface have also been enhanced.
Design of CNC machining
CNC machining is a universal machining process, especially parts that can be cut and machined can be achieved through CNC, from simple shape shapes to complex curved structures. However, as with every manufacturing technique, CNC machining has some design limitations. We break them down as follows to ensure that your products are optimally designed to better fit the CNC machining process.
General Tolerance
When designing parts, the size of each part is different according to the application environment, working conditions, etc., and the requirements for the machining accuracy of the workpiece are also different. Although CNC machining can achieve very high machining accuracy, we should also be aware that demanding machining accuracy and accuracy (strict product tolerances) usually mean Longer production times and higher costs. If a specific tolerance is not specified in the product design, we recommend choosing at the following levels.
Permissible deviations in mm for ranges in nominal lengths
|
Tolerance Class Designation(Description)
|
fine
|
medium
|
coarse
|
very coarse
|
0.5 up to 3
|
±0.05
|
±0.1
|
±0.2
|
--
|
over 3 up to 6
|
±0.05
|
±0.1
|
±0.3
|
±0.5
|
over 6 up to 30
|
±0.1
|
±0.2
|
±0.5
|
±1.0
|
over30up to 120
|
±0.15
|
±0.3
|
±0.8
|
±1.5
|
over120upto400
|
±0.2
|
±0.5
|
±1.2
|
±2.5
|
over 400up to 1000
|
±0.3
|
±0.8
|
±2.0
|
±4.0
|
over 1000up to 2000
|
±0.5
|
±1.2
|
±3.0
|
±6.0
|
over 2000 up to 4000
|
--
|
±2.0
|
±4.0
|
±8.0
|
The highest precision of our equipment is 0.001, and the recommended most precise machining requirements do not exceed +/-0.005mm
Interior angle
All internal vertical edges of our products need to have rounded corners instead of right angles. This is because the tools used in CNC milling are cylindrical, which means they cannot produce inner right-angled edges. The fillet required by this process is called the inner corner fillet. When designing parts, the larger the inner corner fillet, the more efficient the production process. Because of the larger fillets, larger diameter milling cutters can be used to increase milling speed, and fewer swaps can be made to improve accuracy.
Undercut
Undercut cannot be machined with standard milling cutters, so the use of retract slots for parts should be avoided when designing CNC machined parts. In particular, for non-standard inner contour shapes, customized machining tools are required, which will greatly increase processing time and costs. Secondly, if undercut can not be avoided, due to the limited length of cnc tools, the undercut can not be too deep. If they are too deep or the location is difficult to reach, they will not be able to be produced because the CNC tool cannot reach the machining location.
Chamber wall thickness
CNC machining requires your part design to meet minimum wall thickness requirements. In general, it is recommended to choose the thickest possible and avoid very thin or characteristic walls. This is because CNC tools processing thin-walled parts will cause vibration deformation, which may cause interruptions or damage, and the size is out of specification. The standard minimum wall thickness for CNC machined metals is 0.030" (0.76 mm) and for plastics is 0.060" (1.5 mm).
Thread
When designing parts, it is useful to choose the largest possible thread size because smaller taps have a higher risk of breaking during production. If possible, avoid using deep hole threads as they lead to higher production costs, especially when custom tools are required.
Metal
In principle, materials with high hardness are easier to process because better processing accuracy can be obtained, but they are limited by the hardness of processing tools, so the hardness of the generally recommended parts is 8 ~ 60HRC, and for metal materials, the hardness is greater than stainless steel Followed by cast iron, followed by copper, and finally aluminum, while the processing of ceramics, plastics, etc. belongs to the processing of non-metallic materials. Fast production time.
Polymer
Although CNC can process thermoplastics, the material properties of polymers still have many difficulties for CNC processing. First, due to poor thermal conductivity, many thermoplastics melt or bend when in contact with CNC milling machines or drill bits. Secondly, the processing of plastics, because the hardness is low, the size accuracy caused by the knife during product clamping and processing is not high. For those parts that do not have special requirements for the strength and hardness of the metal, thermoplastics can provide a cheaper alternative.
Cost optimization of machined products
Simplify product design
Simplifying product design while taking into account functionality usually saves production time and reduces production costs. Because the manufacture of complex structures and surfaces often requires complex longer passes, more layering to obtain the same fine contour quality. This means higher production costs.
Reduce cutter changes
Using the same milling machine machining features, larger and same internal fillets, can reduce the number of tools used to reduce machining time. For example, if a workpiece needs a 10mm end face milling cutter to process some features, it also needs a spherical milling cutter to process a curved surface, and a 2mm milling cutter to process a fine groove, which will require repeated tool changes and reduce the machining efficiency
Proper material selection
The choice of raw material for machining can have a significant impact on production time and costs for CNC machining. If possible, choose a material with good processability, such as brass or aluminum. For those applications that do not require metal hardness and strength, CNC machining of engineering plastics like PMMA and ABS also helps to reduce costs because the material blank is cheaper, and the processing efficiency is higher.
Tolerance and wall thickness
Higher tolerances and thinner wall thicknesses also increase THE CORRESPONDING CNC machining costs, as it takes time to achieve higher precision cutting. If your product or component can accept a larger size range, choose a lower tolerance to reduce production time and costs. The same is true for wall thickness: a larger wall thickness margin should be chosen.
Choice of surface treatment
Surface treatment is often the final stage of the CNC machining process, which can also affect the cost of your entire project. Choosing less surface treatment for your part or product can lead to better time and cost efficiency. FCE can recommend to you how to optimize the surface treatment to balance the conflict between cost and quality according to your final needs.
FCE Machining services
FCE facilities are equipped with the most advanced and highest precision 3, 4 and 5-axis CNC machines, which allows us to complete your order in record time
1. 15+ year work experience engineers
2. Fastest 5 days delivery
3. Prototypes can be machined as quickly as 1 day.
4. More than 200 metals and plastics material available in stock
5. Tolerances as low as +-0.005mm
6. ISO 9001: 2015 certified factory
7. 40+ CNC machines
8. 50,000+ machined parts per month
We cooperated with many world top 500 companies and awarded good responds always.
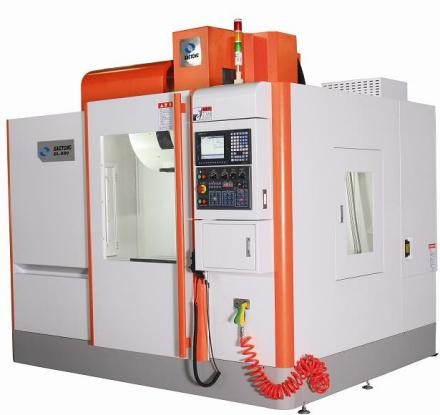
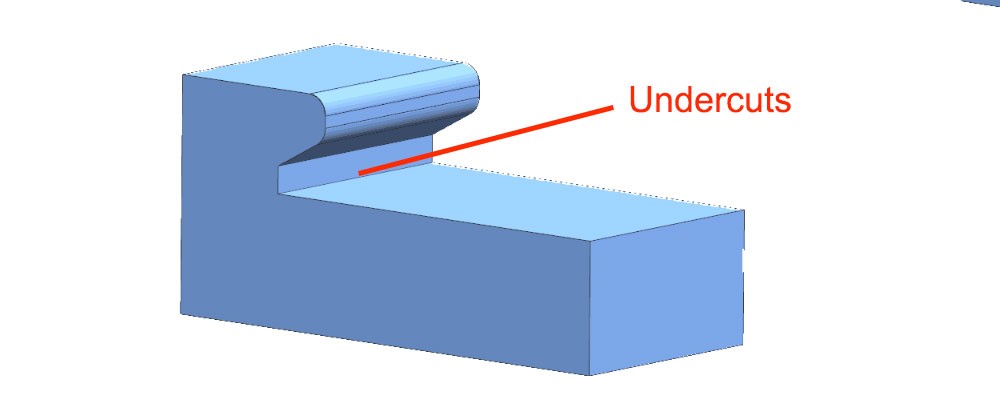
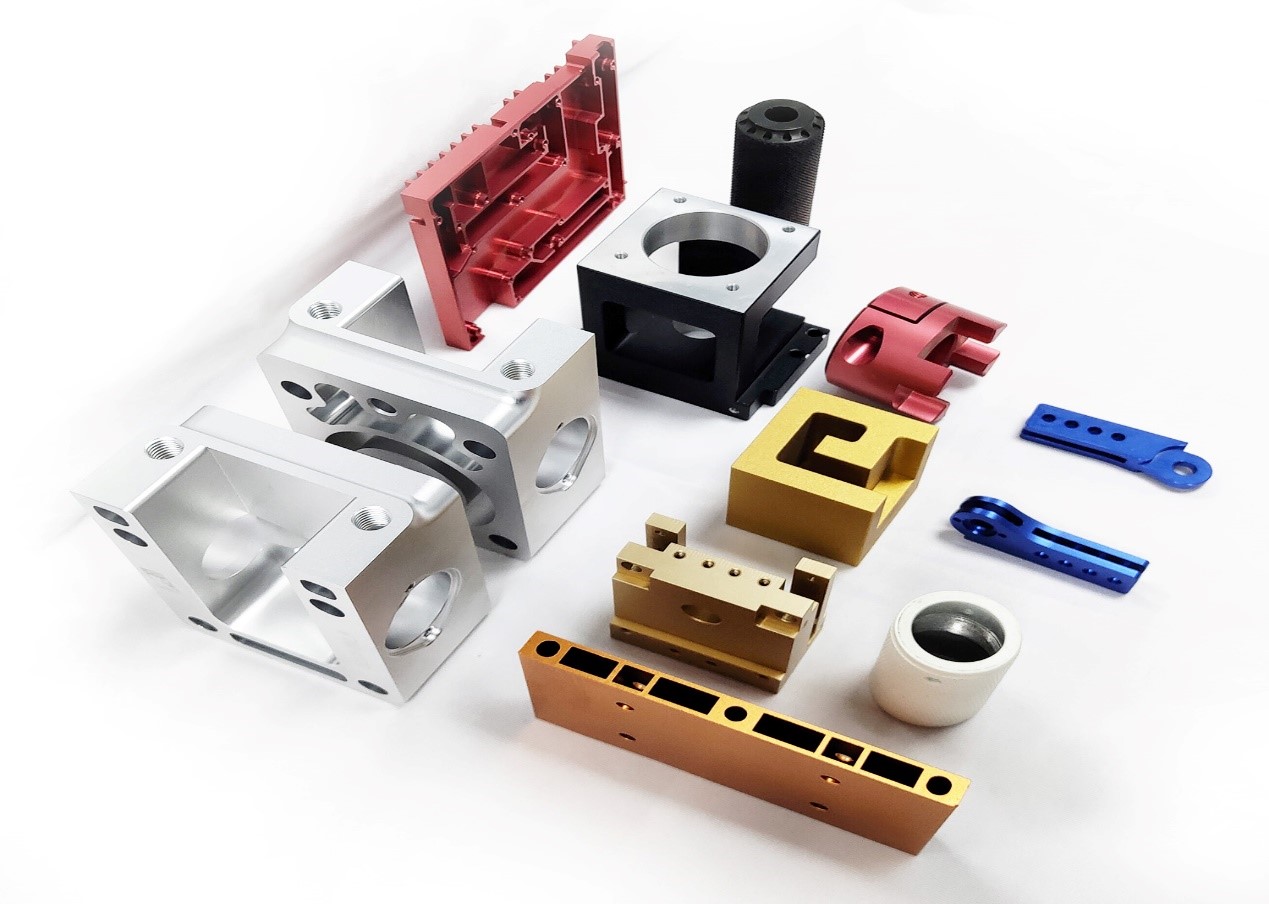
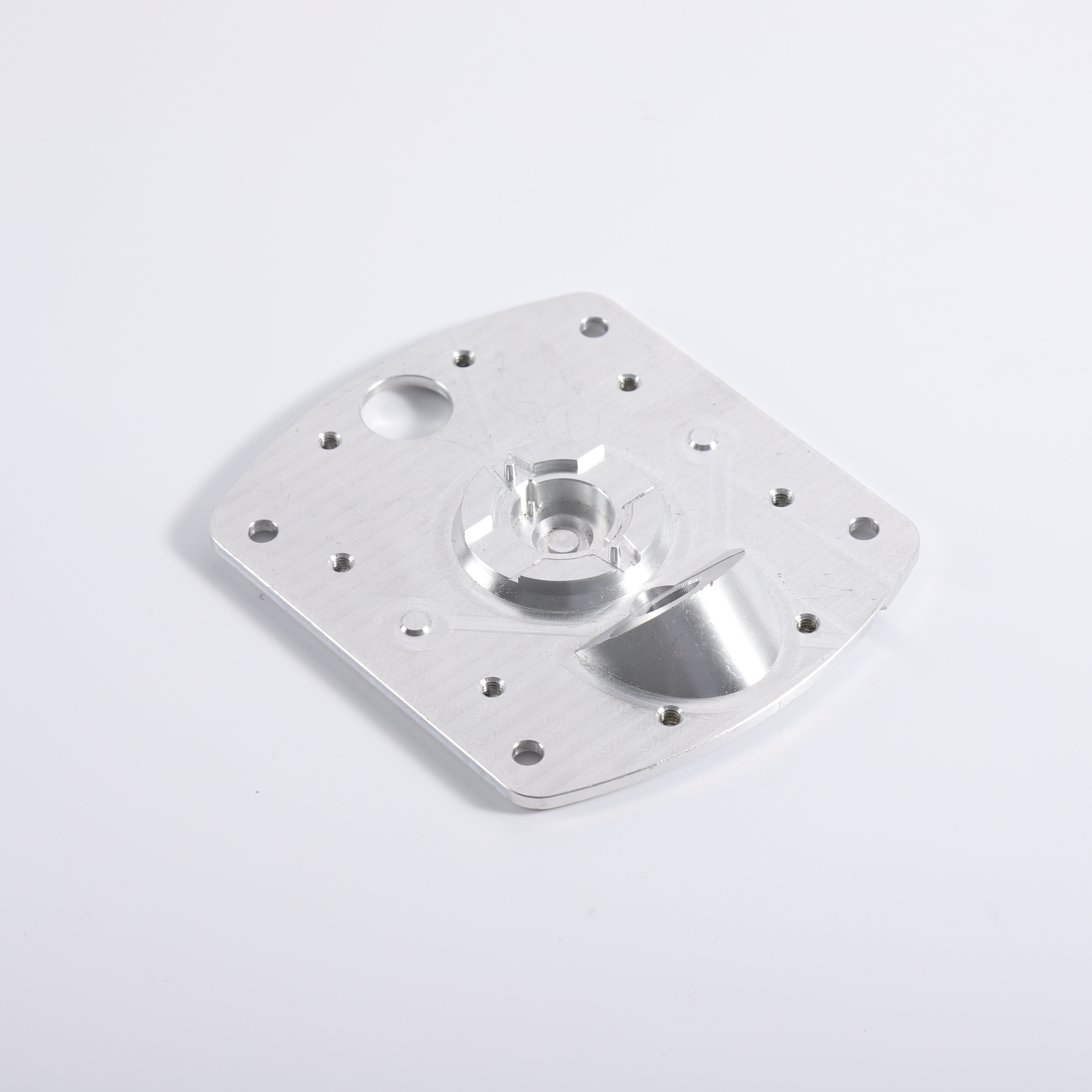
Cnc Milling,Cnc Milling Services,Custom Cnc Milling,Cnc Lathe And Milling Machining
Suzhou FCE precision electronics Co., LTD , https://www.fukeyifcesz.com